Data Flow
Overview
The only data connection between the PC and the hand is a 100Mbps EtherCAT cable. EtherCAT is an open high performance Ethernet-based fieldbus system. The EtherCAT cable enters the hand at the elbow, and connects to an EtherCAT bridge which converts the signal to E-Bus (LVDS) which is suitable for connection to the palm as it needs no magnetics.
Motor hand:
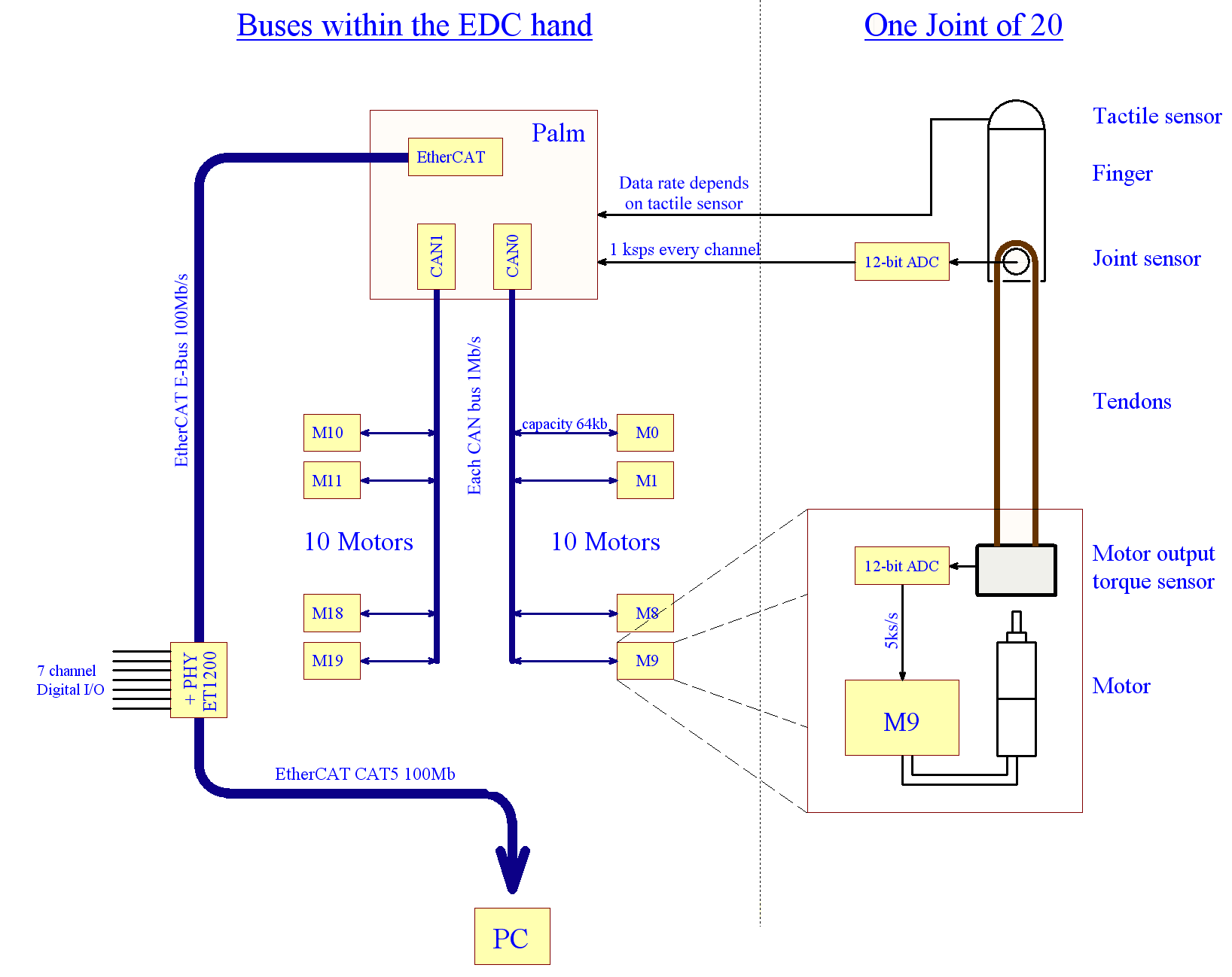
Two CAN buses are connected to the palm, and each serves 10 motors, giving a total of 8kB/s bandwidth to/from each motor. An SPI bus serves each finger, allowing the palm to sample all joint sensors at 1000Hz.
Palm
The palm acts as the main data hub, dealing with all EtherCAT, CAN, and SPI communication.
Fingers
Each finger is identical. It contains four analogue Hall effect sensors which measure the position of each of its four joints. Three of these sensors are sampled by an ADC in the finger, while the fourth (J4) is sampled by an ADC in the palm.

The proximal phalange contains the ADC, which is connected to the palm by SPI. It also houses the connectors for the middle phalange and the tactile sensor.
Thumb
The thumb contains six Hall effect sensors to measure the position of its five joints. The base joint with its large angle range needs two sensors to fully cover the range.
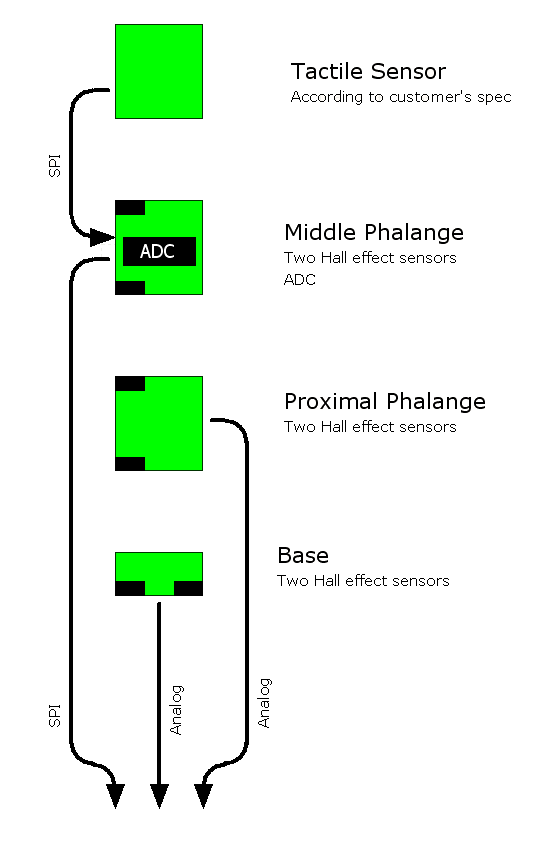
Only the middle phalange of the thumb contains an ADC. The other two phalanges return analog signals which are sampled by an ADC on the palm.
Motors
When in torque control mode, each motor MCU samples its own torque sensor at 5000Hz, and updates the motor PWM signal at the same rate, according to its internal PID control loop. New force demands are sent to the motor MCU every millisecond. When in position control mode, the force control loop is switched off, and the host simply sends PWM demand values to the MCU every millisecond. These are implemented immediately. Requests for sensor data are sent to the motor MCU every 2 milliseconds, and corresponding values are returned immediately.
Analogue sensor filtering
Hall effect sensors naturally produce noise, and so need a simple RC filter. The filter produces a flat response to 100Hz, allowing for an undisturbed joint angle signal up to rotation speeds of 90º per 0.025sec.
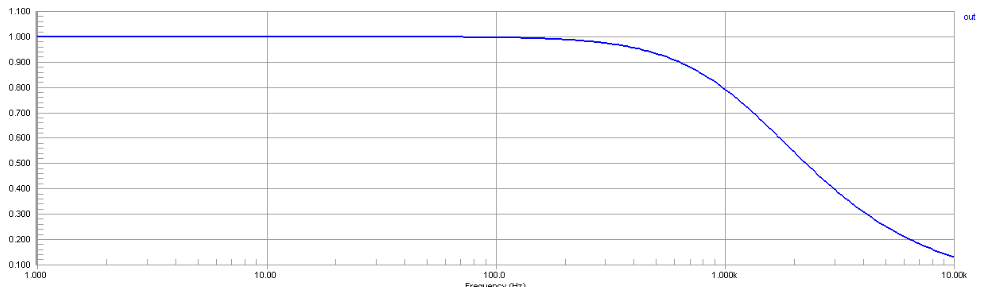